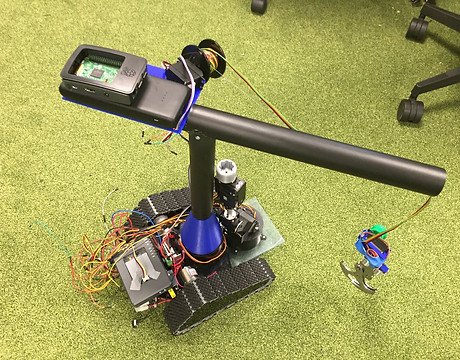
Fuel Cell Retrieval
System
As one of the central mission objectives, retrieving the fuel cell required the integration of several sub-systems. A way of detecting the fuel cell location, a hook mechanism to collect the fuel cell and a method of raising the cell to ground level once collected. In order to provide a robust and adaptable system, a mixture of OpenCV image processing and an ultrasonic sensor were used to identify and collect the cell. A durable metal hook was designed using Solidworks and produced at the team's in house workshop. When operating with OpenCV image processing the crane demonstrates level 5 autonomy.

Design Features
Fuel Cell Localisation
A combination of a RaspberyPi Cam v2.0 camera module and RPi 3 B+ running a Python version of OpenCV image processing are used to detect the position of the fuel cell. A function, named moments, within OpenCV allows the software to compare the number of coloured pixels either side of a user calibrated point. When there are an equal number of red pixels on either side of this point the hook will be centered above the fuel cell.
Hook
The gravity hook inspired design is attached to the crane using high strength Nylon line. 3mm thick steel ensures a durable claw, making it suitable in the harsh mission environment anticipated. The claw, designed to grab the cell handle, can successfully attach across in over 320 degrees. With the addition of an ultrasonic sensor, servomotor and RPi microcontroller it can carefully collect the cell, ensuring it is still attached it is raised.
Ultrasonic Ranging
The hook mechanism relies heavily on the ultrasonic sensor to detect how close the hook is from collecting the cell. The sensor provides distance measurements back to the RPi micronctroller, which in turn signals the servo to hold the hook over. When the hook gets within 16cm of the fuel cell the RPi instructs the servo to close whilst also stopping the reel from lowering further.
3D Printed Base
To realise the crane as intended Team Helios employed modern 3D printing techniques to prototype and a produce bespoke base. Lightweight, durable and most importantly perfectly fitting, the crane base is an example of the workmanship and considerations made by the team.
3D Hook Cradle
To house the ultrasonic sensor and servo required to operate the hook, a 3D printed cradle was designed and produced. A slot stops the crane twisting whilst a ultrasonic sensor mounting ensures clear view of the fuel cell location. Further supports keep the servo in place whilst allowing for safe wire placement
Capabilities Demonstrated
-
​Communication Failure Management - Remote access to the RaspberryPi micro controller, via VNC software, allows the operator to take control of the crane and its functions at any time if hardware based instructions fail to operate. Additionally the Pi can be set up to require no manual intervention using a GPIO in from the MyRio with the fuel cell location being identified by the route finding algorithm.
-
Autonomous Operation - The crane can detect the fuel cell, via image processing, without any manual intervention, stopping the motors and lowering to the cell. With the ultrasonic sensor and servo, the hook is capable of deciding when to close and reel back. In the event of a failed collection the crane can reattempt collection repeatedly.
-
Collaborative Platform Integration - The system integrates an ultrasonic sensor, 3 servo motors and a RaspberryPi. It also has the potential for a hard wired connection to the MyRio on the Kratos.
-
Careful Handling - The crane raises the fuel cell at a much slower speed than it initially drops in order to reduce sway and likely hood of tilting. The hook mechanism, having the ability to reattempt collection and only engaging when in correct range, also demonstrates careful handling.
-
Identify and retrieve fuel cell - The crane is purely designed to retrieve the fuel cell. Upon a successful implementation and in conjunction with the image process mapping, which identifies the cell location, this capability is achieved.