Crossing Complex Enviroments
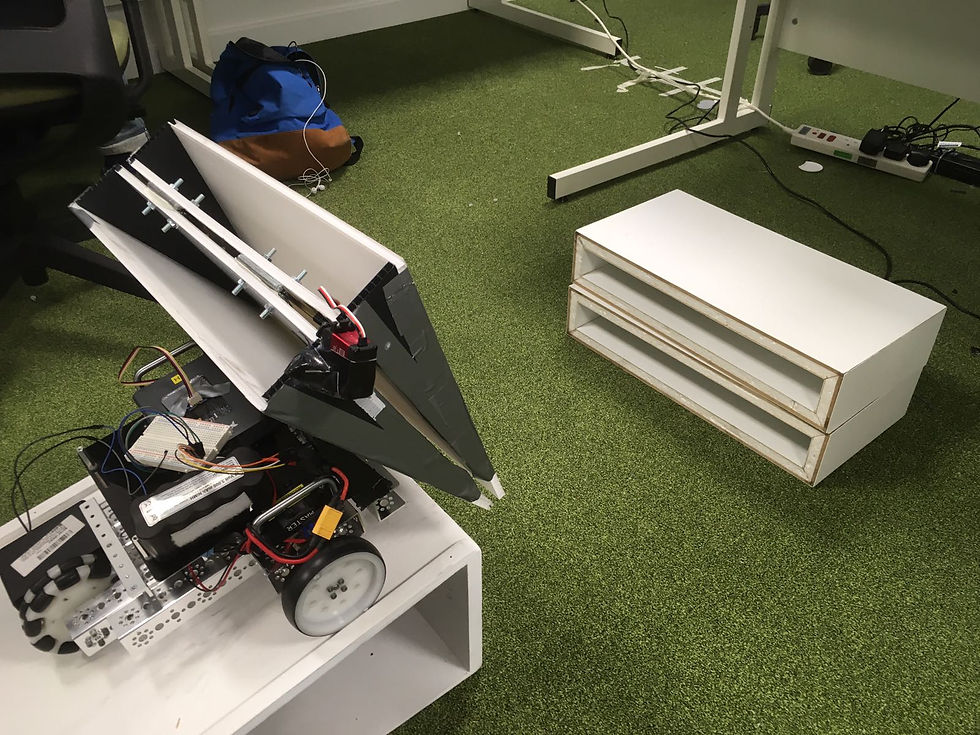

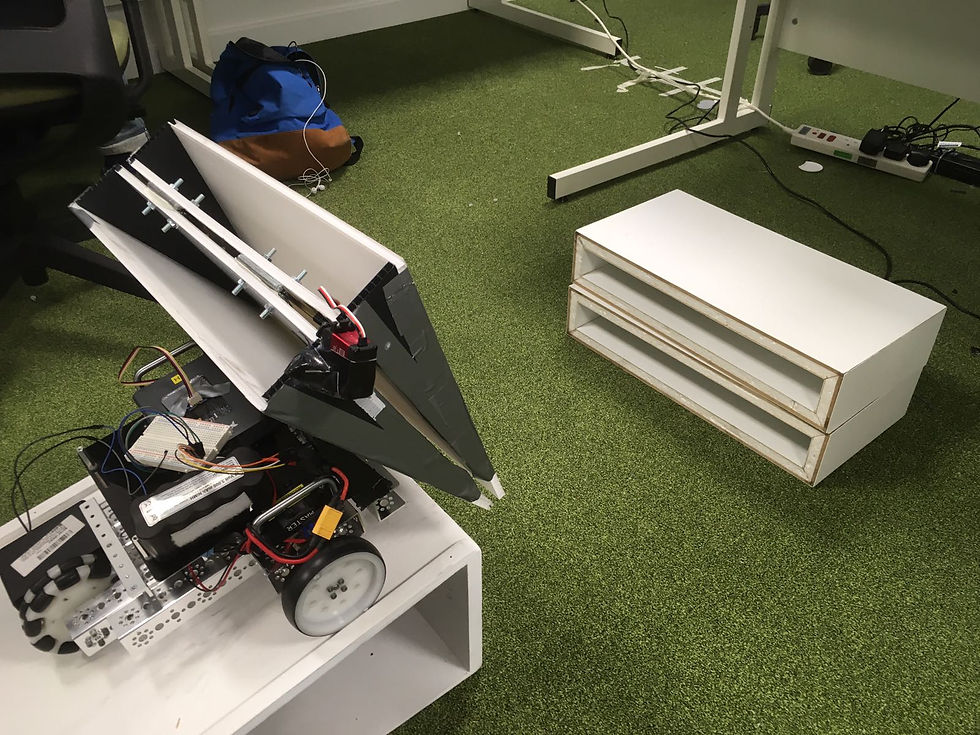
Autonomous Bridging Deployment
The bridge sequence is triggered by the front mounted ultrasonic sensor reading that the DaNI has encountered a potential fall, stopping the robot so that it does not fall and then prepares to lower the bridge.
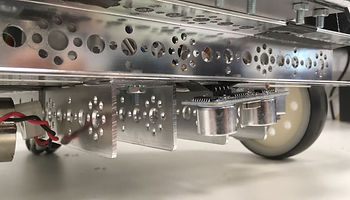
The control centre then sends a Bluetooth signal to the Arduino housed in the bridge to unfold vertically. Using a Bluetooth signal allows the control centre to deploy the bridge even if there is communication failure with using the WiFi.
The DaNi robot can then lower the bridge into place by turning the servo connected to the steel pick-up mechanism at the front of the robot. The bottom of the bridge was made to be slightly less than 50cm so that it fits in the gap and will not move when the robots drive over it.
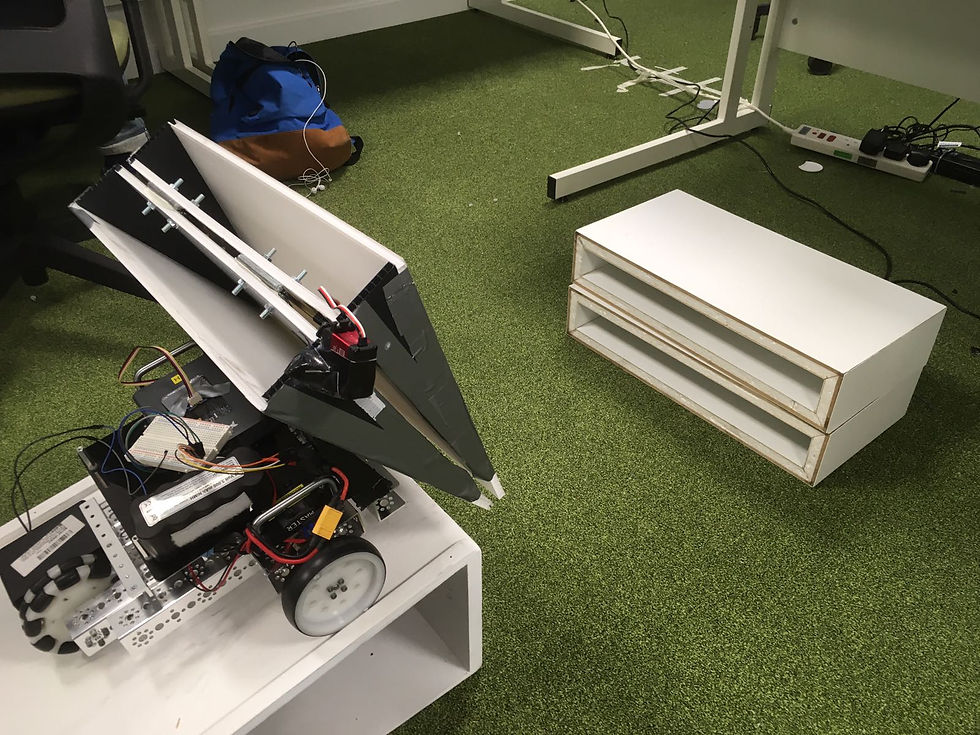

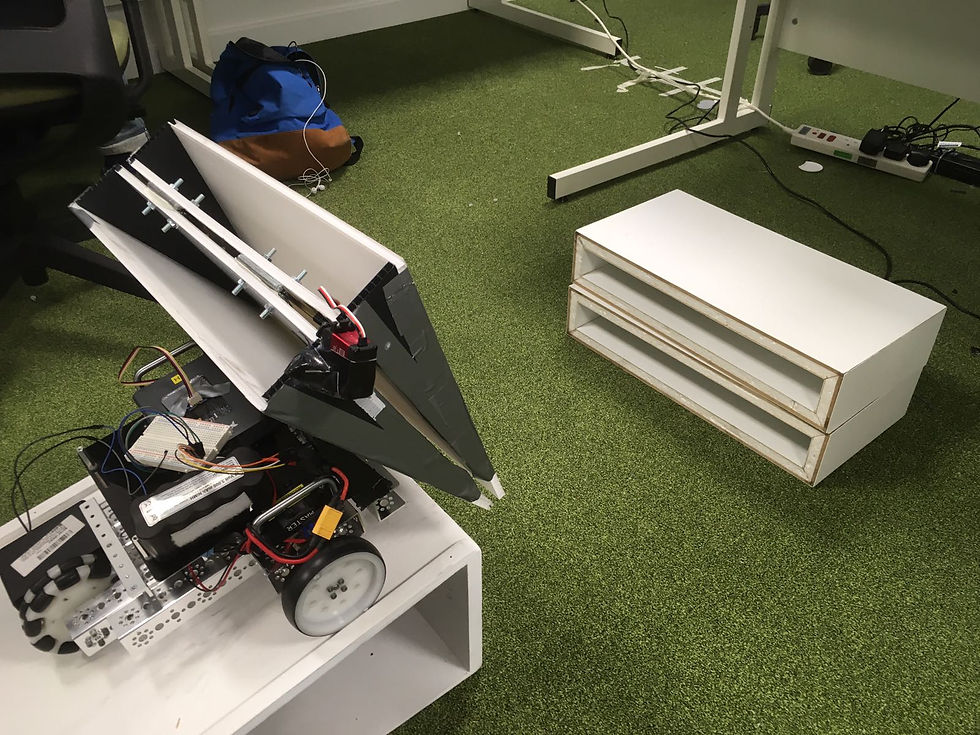
The bridge is made from 6mm corrugated plastic designed on AutoCAD with a connected puzzle design to provide a strong, rigid bridge for the robots to safely traverse.
Capabilities Demonstrated
-
Communication Failure Management - The bridge deployment system can be connected to manually by any Bluetooth device such as a tablet to tell it to unfold and be laid in position to cross.
​
-
Crossing Complex environments - The main purpose of the bridge is to allow the robots to traverse difficult terrains they may encounter. The bridge can be used to cross a gap of up to 50cm and can bear a load of up to 20kg.
​
-
Collaborative platform Integration - The full bridge deployment system utilises many different technical elements that are required to interact effectively with each other. The system makes use of an ultrasonic sensor, feeding data to a MyRio, sending updates to the control centre when it detects a potential fall followed by a Bluetooth signal to the bridge electronics to unfold and deploy.